Top 5 Ways Robots Help Your Finisher Operations
April 24, 2020
It’s a competitive world out there. Growing demand for industrial goods of all kinds has been putting pressure on all kinds of manufacturing operations to become sleeker and faster. Shorter lead times are the new order of the day, but how can one maintain or even improve quality in the face of such mounting pressure?
One answer for manufacturers and finishers is to use a painting robot. While presenting an initial need for capital investment, these devices save money in the long-term, and create several other benefits while allowing production to be almost continuous. If you operate industrial paint booths, then you should know exactly how these robots can help your operation.
1. Multiple mounting methods
Choose to mount the robot either on the floor, wall or ceiling, depending on your space restrictions and exact needs. Large objects in need of paintwork will benefit from a ceiling- or wall-mounted robot, but where space is not an issue, a simple floor-mounted robot will get the job done easily. In this way, you can have your robot installed exactly where it needs for an optimum finish on every product.
2. The help you deploy your workers and resources more effectively
If you are running a high-volume production facility with continuous processes and large products like vehicle bodies, then you can install a system where robots can spray from both sides and no human input is needed at all, freeing up workers for other tasks.
Even in a low-volume facility, you can use robots to streamline production by having workers load and unload parts from a turntable before and after they pass through the booth to the painting robot for finishing. It means your workers are less exposed to the paint spray and the operation can run more smoothly.
3. You can save on energy costs
Energy is a continuous and unavoidable source of expense, but paint robots can help to save energy when you couple them with recirculating spray booths. By recirculating exhausted air back into the paint booth, you lower the energy requirements because you don’t need to keep inputting new fresh air. This process ordinarily would be problematic because the recirculated air brings with it volatile organic compounds that would demand any human workers wear heavy-duty protective gear. With a paint robot at the helm, you don’t need to worry about that.
4. There will be a trickle-down effect of savings
Many of the advantages we mention above have a long-term financial and operational benefit when applied in the long term. Human workers, for example, will risk compromising on the evenness or quality of their paint finish as their shift goes on longer and longer. A paint robot, on the other hand, can operate in exactly the same fashion over and over for protracted periods without compromising even an iota.
The arm speed stays consistent, the angles of movement and spray and other physical movements are consistent. Over time, this ensures a steady increase and consistency in quality of output. That makes quality control far easier, and ultimately lowers costs as a facility is able to finish more product faster and to a higher consistent standard.
5. Robots get where humans miss
Finally, in objects with awkward corners, nooks, crannies and other angled spots that are hard to hit just right by hand, a painting robot can ensure precision and evenness across the entire surface. Contours easily escape the manual handiwork of humans, but find it hard to escape the precision, computer-guided work of a painting robot.
In the end, to maximize these benefits, you also need to work with a top supplier of paint booths with the expertise to help you install and maintain systems that suit your operation and its precise needs. Talk to us today
at Ecotech Systems to find out more about our advanced painting and finishing equipment.
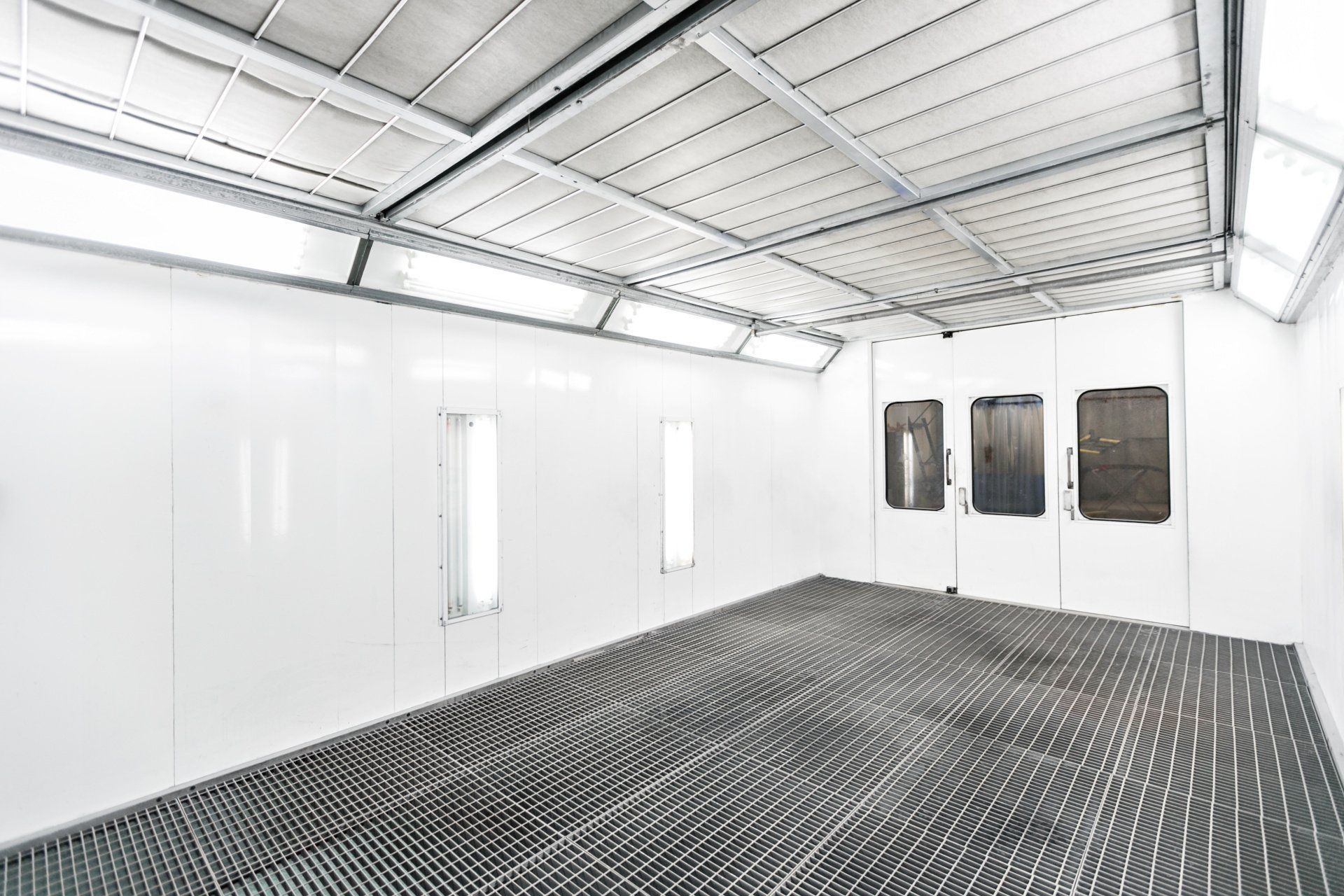
Paint Booth Design - What are the Key Elements When you’re exploring the diverse world of paint finishing, the paint booth is a piece of kit that you simply won’t be able to ignore. Whether you’re a new operation looking to set up shop, or a more established outfit looking to expand or update your facility, knowing the key components of paint booth design is essential. Let’s first be clear on what we mean by “paint booth.” These are purpose-built environments for the safe and effective application of paint. Their main advantages over older-style application methods include the automatic removal of dangerous vapors and other contaminants to create a safer environment for painters, as well as better chances of nicer finishes on the paint work. There are 5 key component areas we will explore below: paint booth walls and doors; air intake plenum; exhaust chamber; air make-up unit (AMU), and the manometer. Paint Booth: Walls and Doors When looking at paint booth models, you’ll find either single-skin or dual-skin walls. The former is better for use when the budget is tighter, but without compromising on strength and rigidity. The latter is typically more durable and longer-lasting, with added insulation. In both cases, you’ll likely find the walls are white, for better reflectivity and visibility in the workspace. You might think that a door is just a door. It just needs to open and close, right? In fact, spray booth doors are specially designed in roll-up, swing and tri-fold designs. The design of the door you need depends on how you’re working. If you’re using non-pressurized booths, for example, then you’ll likely need filtered doors. Air can pass through them, but additional filters stop unwanted contaminants from getting in. If the booth is pressurized, on the other hand, then you’ll use solid doors, with air entering through the air intake plenum. Air Intake Plenum The intake plenum brings air into pressurized booths that include solid, sealed doors to maintain a dust and dirt-free environment. The air may flow from the floor or from overhead depending on the exact design of the booth. Filters within the system remove dust and other contaminants before it enters the space. Exhaust Chamber The keywords for the exhaust chamber design include: crossdraft, semi-downdraft, side downdraft, and downdraft. The exhaust chamber works with the exhaust plenum and exhaust pit, both of which are part of the air-removal stage of overall circulation. The location of the exhaust components depends on the keywords we mentioned above. In a crossdraft design, for example, the plenum is in the rear. You’ll also find the exhaust pit in the downdraft design. Regardless of their exact specification, they perform the same basic function --- exhaust and filter air from the booth in a way that protects the painter and the other critical components of the booth like the fans, stack and plenum. Air Make-up Unit (AMU) This is another key part of circulation. It wouldn’t be much good if the exhaust described above was pushing the air out faster than it could be replaced. This is where the AMU comes in. It maintains a constant air flow and temperature and will restore exhausted air in equal measure. Manometer Finally, there’s the manometer. This is used to show when you need to replace the paint filters. Over time, overspray and other particles will build up on the filter and render it unusable. The manometer tells you the current state of the filter, and thus you’ll always know when to change them. Manometers range from relatively simple gauges to more complex photohelic and magnehelic designs. Ask the Experts In the end, choosing the right kind of paint booth design for your operation will require considerable expertise in support. Here at Ecotech Systems, we can provide that support. Get in touch and learn about which booths will suit your facility best.
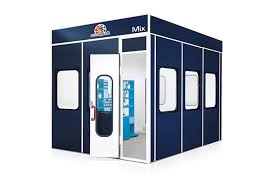
It’s interesting that we still use sayings like “watching paint dry” to refer to things that are boring. Those who understand paints know that even when paint is sitting still and waiting to be used, it can all get rather exciting, and dangerous. The majority of paints are either flammable or otherwise combustible, which is why adherence to the proper standard and guidelines on storage is absolutely essential. Below we’ve prepared some key suggestions on how to ensure that your own paint finishing facility is up to scratch when it comes to safe paint storage. Augmenting the Facility If you have the space, budget and relevant permissions from local authorities, then creating a dedicated paint mix room and/or hazardous material storage building will be a huge benefit. Having a dedicated space for these operations means you disrupt other parts of your facility less. Let’s say you are currently performing mixing in your spray booth, that’s valuable finishing time that you are losing to an operation that would be better --- and more safely --- done in a dedicated space like a paint mix room. Other benefits to adding these facilities come in the potential increases to the maximum amount of stored paint you can keep on-site. We’ll deal with that below. Know Your MAQ Numbers The maximum allowable quantities (MAQ) of paint you can keep on-site depends on the class of paint you’re using. You can actually find these numbers within the International Fire Code, and they are classed within groups “Combustible Liquid,” “Flammable Liquid” and “Flammable Liquid, Combination.” Storage in liquid gallons can range from, for example, as high as 13,200 gallons for class IIIB combustible liquids in a closed system, to as low as just 10 gallons for Class IA flammable liquids in an open system. You can increase your MAQ by up to 200 percent by meeting the following two requirements: Install a working automatic sprinkler system Store materials in an enclosure with exhausts such as a paint mix room (described above) Arranging Your Paint Mix Room(s) In larger facilities, it makes sense to install multiple paint mixing rooms if possible, to both speed up safe operations and potentially increase your safe and legal paint storage capacity. There’s no legal limit on the number you can have. The key to maximizing efficiency is relative position of the mixing room to the spray booth. If it’s within 6 feet of the spray booth, you can store 2 gallons per square foot or 120 gallons (whichever is less). If it’s further away, the 2 gallons per square foot rule applies still, but for any class of paint. If you are storing paint in your spray booth, currently, then you are only enjoying a maximum of 60 gallons of storage. The electrical area classification for your paint mix room will be the same as for your spray booth – Class I, Division 1. Controls for Explosions If you are storing Class IA or IB liquids, and have exceeded the MAQ, then the IFC requires you to have explosion control methods in place. A common choice is deflagration venting placed along exterior walls with vents to allow for exterior venting. Another choice is reducing the concentration of hazardous materials. Work with Specialists You very likely know your finishing business very well, but if you’re planning the kinds of modifications that we’re describing above to increase your capacity and streamline your operation, then a little extra help is useful. Talk to us here at Ecotech Systems about installing your paint mix rooms and how to arrange them to suit your exact needs.
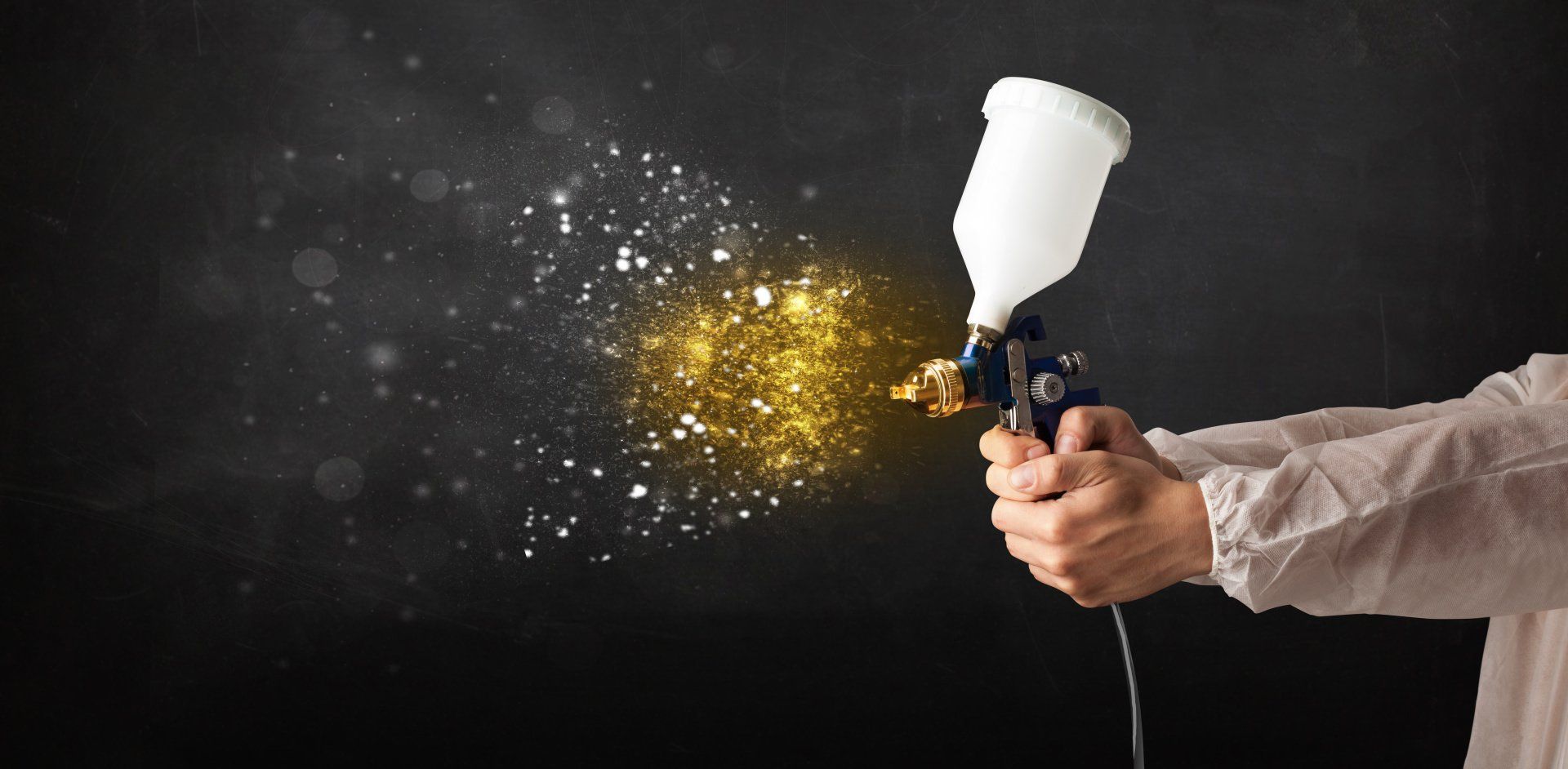
As ever, the automotive and industrial world and its materials are changing. Over the past several years, many sectors have been making a shift from durable solvent-based paints to more modern and innovative waterborne paint. Broadly speaking, the move is largely environmental, but there are many good reasons to switch to waterborne paints, in fact. The main problem for some enterprises, especially in the industrial coatings industry, is how to make this transition both safely and effectively. Even though some 80 percent of household paints are now waterborne, according to information from the US Coatings Blog and originally from the Paint Quality Institute, some in the heavier industries have resisted making the shift. This is often because of fears of increased cost or general upheaval that might interrupt productivity. In today’s article, we’ll demonstrate not only that the move is safe, but also cost-effective and beneficial to your overall operation. Difference Between Solvent-Based and Waterborne Paints Obviously, the two paints perform the same basic coating function, but the main difference lies in their makeup, in particular the element used as the base solvent. In solvent-based paints, volatile organic compounds are used as the solvent. This is what gives them that more durable finish. As the name suggests, waterborne paints use water as the main solvents. Besides that, both paints use pigment, filler and binder in their formula. There is some considerable difference also in how they appear and smell when applied, and when you want to remove them. Waterborne paint is easier to remove, whereas solvent-based paint requires thinners, turpentine and similar chemicals. The solvent-based paint also carries a very powerful odor that can cause headaches, dizziness and general feelings of malaise if not used in a well-ventilated area. For this reason, it has largely been used for outdoor coatings, especially given its resistance to nature’s many elemental forces. Making the Shift – Some Things to Remember When you’re in the automative and industrial coatings industry, making this shift isn’t just a question of loading up different paint into your spray booths. Below are all the important things you have to consider and act upon when changing to waterborne paints: 1. Paint Gun Material The paint guns you’re using have to be made from materials that are corrosion-resistant. Waterborne paint tends to get stuck more often than solvent-based paint, and so you’ll also have to find different cleaners designed specifically for removing and cleaning up waterborne paint. 2. Time Shifts in Curing If you’ve been using solvent-based paints for some time, then you’ve probably built a schedule based on the curing times of those paints. Waterborne paints take longer to cure, so you may have to adjust your processes or shift patterns to match those times. There are some solutions for this problem, such as the Accudraft Xcelerator, which can boost energy efficiency and lower curing times. 3. Humidity is the Enemy Whereas solvent-based paints are more resistant to the various weather and environmental conditions of almost any location, waterborne paints in their current form are a little more susceptible. In particular, humidity is very bad because it prevents the water from evaporating during the curing process. You will have to ensure you are able to control the humidity in your workspaces. 4. You’ll Still Need the Fans Probably the most obvious difference, and advantage, of waterborne paints is their lack of nausea-inducing odor. You might believe from this fact, as well as the name waterborne that the need for fan ventilation and other protections for painters aren’t necessary. That could represent a great financial saving. In fact, the opposite is true. You still need to use effective ventilation, because the content of volatile organic compounds (VOCs) is greatly reduced, their shadow does remain in the undercoats and topcoats. As experienced coatings providers will know, good airflow in the work area is absolutely essential, regardless of the quality of the paint being used. It’s important for the painters, first of all, but also for the process itself to remove flammable and/or combustible materials. 5. Waterborne Paints Are Not Weak While it could be argued that waterborne paints have yet to catch up to the outdoor robustness of solvent-based paints, it cannot be said that they are weak. In every other condition, waterborne paints are as durable, if not more durable than solvent paints. More importantly than that, they have other strengths that are good for both the environment and your business. The chemical makeup of waterborne paints generally makes them less toxic and less polluting to the air. Beyond that, they are cheaper in the long run because as you use them over time, the amount of waste you have should reduce, thus bringing big-picture costs down. You also will notice savings based on the fact that you need less waterborne paint to get the job done than you do solvent-based paint. Finally, it must be said that waterborne paints are brighter, more vivid and pleasing to the eye than solvent-based paints. From the first time you start using them you should notice the difference. As you make your own transition to waterborne paint, it’s important you work with a partner that knows the industry well and can help prepare every stage of your processes to integrate these new substances more seamlessly. For that, look to Ecotech Systems and our array of products to best suit your needs.
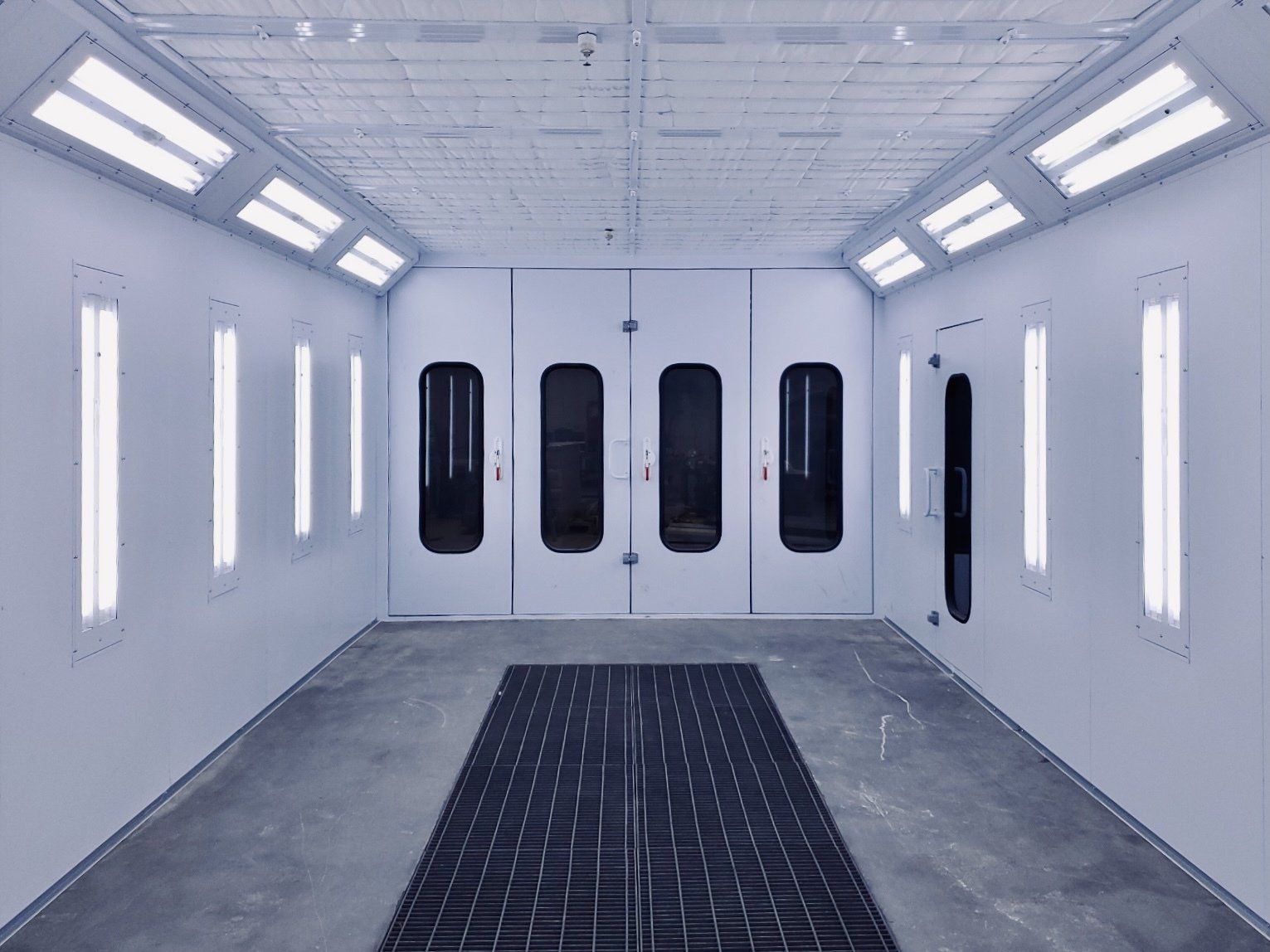
A paint booth is an extremely effective tool, but also a complex and expensive piece of equipment. They revolutionize the processes of painting. One of their key components is the filter. In today’s piece, the team here at Ecotech Systems will explain what these filters do and why it’s essential to keep them well-maintained. What are Paint Booth Filters & What Do They Do? In short, paint booth filters are a protective measure for many of the system’s components. They come in three main forms --- air makeup; intake; exhaust --- and their function is to remove various contaminants such as particulates and dust. Below is a brief summary on how each system works: Air makeup filters : Located in the air makeup, these filters remove large particles from the air before they can get into the paint booth cabin. Intake filters: Found in downdraft and cross-draft booths, using a diffusion-type material polyester or linked panel filters to keep contaminants from the coatings. Exhaust filters : These work on ensuring clean air leaves the cabin, helping to keep dangerous chemicals from being circulated in the atmosphere outside the booth cabin. Importance of Proper Filter Maintenance The simple fact of the matter is that a paint booth will not work either safely or effectively when the filters have become worn, defected or otherwise unable to perform their function. If proper maintenance is not maintained, you run the risk of at worst contaminating your work environment and endangering members of staff, or at best allowing damaging contaminants to enter the coatings. There are several must-do tasks in order to ensure optimal efficiency of your paint booth filters: 1. Ensure you have a working manometer and use regularly A typical quality filter will need changing after 100 operating hours, which for many will equate to roughly 2 or 3 working weeks. You should therefore confirm the need for changes using your manometer to see when the filters are about to become overloaded. If you wait too long, you raise the risk of negative effects. 2. Invest in high-quality filters During challenging financial times, it’s tempting to try to save money and go for budget filters. This can prove counterproductive, however. Cheaper filters typically are less robust and don’t last as long. You may find you have to change them more frequently, thus creating a false economy. An investment in high-quality filters means more efficiency, and a lasting quality filtration action. To that end, it’s worth mentioning that the team here at Ecotech systems has broad experience in this field and is well placed to be your ideal partner in paint booth supply and maintenance. Get in touch with us today to learn more about our products and services, or visit our website – www.ecotechsystems.net
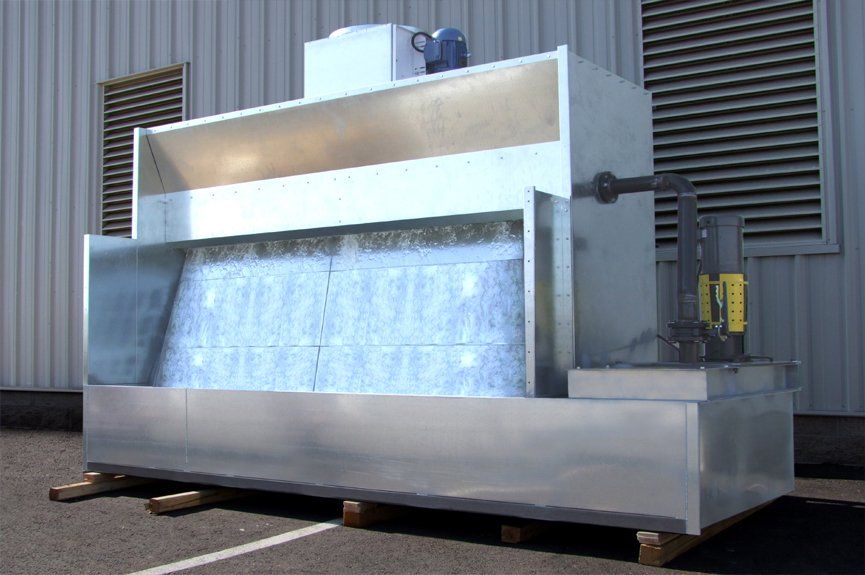
You can’t just go spraying quality powder coats or liquid paints onto any metal parts, you know. There has to first be a thorough and effective washing process that removes contaminants. These contaminants would otherwise prevent the powder coat or paint from bonding with the surface of the parts. What are these contaminants? Typically the manufacturing and transport process of these parts leaves by-products like grease, oil and other dirt on the surface. The best tool for this cleaning process is an industrial pretreatment washer that uses water wash. Such devices bring many benefits to an operation, which we will explore in more detail below. How do industrial pretreatment washing systems work? When you see one set up, it should put you in mind of a car wash operation. The metal parts pass through on a conveyor belt for a multi-stage cleaning --- typically a chemical cleaning stage followed by water and rinse, but sometimes further stages --- before being dried in a recirculating air blow-off system. Specific cleaning materials can be tailored to suit the materials from which the metal components are made. Benefits of these systems: 1. They are labor-saving devices Alternatives to these machines typically involve much more labor-intensive processes that have to manually wash the parts. These workers have to be trained and equipped with hand-held power washers to get the job done. 2. They maintain a consistently high standard of cleaning Another key benefit over manual power washing is that these machines will maintain thorough cleaning standards. Their system-guided targeting and multi-directional nozzles mean every spot on every part gets cleaned the same way. A manual approach means that this consistency is next-to impossible. 3. They reduce water costs A pretreatment washer will use the same amount of water each time it cleans a part. Manual power washers are much less predictable, as there will always be more excess, waste and even misdirected water that gets used to achieve a clean each time. Every drop of water costs your operation something, so efficiently using every drop is a must. 4. They are all-in-1 systems If you manually wash the individual parts, then you also have to find a way to dry them. The beauty of the industrial pretreatment water wash systems is that they come with a built-in drying facility, meaning that all you have to do is feed the parts in, and when they come out they are ready to use. Manual washing means likely taking up one of your valuable low-temperatures ovens to dry them afterward, which could result in a significant bottleneck should you need that oven for other things. Make the investment and reap the rewards Installing a pretreatment washer system requires an initial investment, but like many other automated upgrades, it is a gift that keeps on giving. When you analyze post-installation water usage, wash quality and overall efficiency, you’ll wonder what you ever did without it. Talk to us today at Ecotech Systems to learn more about our industrial washers and how they can benefit your operation.
For any functioning business, the only line that matters is the bottom line. One of the things that greatly impacts your bottom line is waste, and this is something understood very well by those in the world of powder coating. It seems that no matter how you work, things tend to get a bit messy when you’re powder coating something. Even though the amount of waste per item coated may seem infinitesimal, but the issue is when you multiply that waste by the high volume of items that you are coating. Fortunately, there are five things you can do to reduce this waste, thus streamlining your entire operation and boosting your bottom line: 1. Install powder drawers A simple yet novel solution to the issue of waste, removable powder drawers sit under the filters, catching powder after each pulse. Once the job is done, you can just tip the drawers into a storage drum or other unit and then transported. You may not be able to reclaim a great deal of the powder, but the time savings on cleanup are very significant. 2. Use pulse control This technology is an optional addition to the powder collection modules. It’s simple yet impacting, giving much better and more consistent airflow and visibility within the paint booth. It works in tandem with either the drawers mentioned above, or the fluidized powder beds mentioned below. How does it work? The effect stems from a magnehelic gauge located on the side of the booth, which monitors drops in pressure within the booth. Once it reaches the preset level, the filters “pulse” --- shake, vibrate for a very short period --- which causes the powder to fall from the filter and down to either the fluidized bed or the drawer. A neat, high-tech solution. 3. Utilize fluidized powder beds Given that the sheer variety and complexity of shapes make coating perfection impossible, you may find it hard to beat the industry average of 70 percent transfer efficiency. The more complex your part, the harder to avoid waste. One option to mitigate this, however, is fluidized beds, which filters out other parts leaving just powder on the surface, which you can reclaim. 4. Add transfer pumps When you’re wanting to cut down on time wasted shoveling out waste powder from the floor, a simple solution is the installation of a transfer pump. The pump moves powder from the fluidized bed and dumps it into whatever storage container you’re using to catch and process waste powder. If powder reclaim is your goal, then the pump can also be fitted with a filter that catches debris and any heavy sedimentary material that would otherwise leave you with impure and useless powder. 5. Control airflow with manual VFDs A business dilemma exists in powder coating. When you increase airflow, you make the environment safer for the painter, but increase the chance of waste since the airflow pushes more powder away from the object. Conversely, reducing the airflow stops the waste, but creates an unacceptably hazardous environment for the painter. The solution is using manual VFDs. These will allow you to adjust airflow to match the situation. Turn it up when the work is done to remove the cloud of particles that remain behind, but turn it down while the all-important paint work is happening. Follow our tips for an efficient, profitable and better-functioning powder coating operation. When you need help with your paint booths and related systems, you should look no further than Ecotech. We’re on hand to make your operation better and better. Connect with us to learn more.
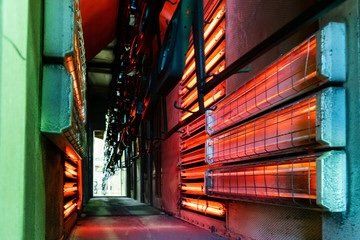
Manufacturers in Texas, Oklahoma and Louisiana are no strangers to the industrial oven. Some producers favor gas burners, and others electric ovens, and the reasons they would give include costs, safety concerns and efficiency at different temperatures. In today’s article, we will be exploring several major factors that should guide your decision in how to choose between gas and electric industrial ovens. As a manufacturer, you may already have one of the factors in your mind, but we advise that you consider all aspects before making your final decision. The impact on your business costs and efficiency will be different depending on your choice, and where your operations are located. Factor #1: It’s true --- gas ovens often work out cheaper In the US, gas generally costs less than electricity, which has helped ensure that the majority of users of industrial ovens will find financial savings when using a gas oven. Yes, a small electric oven is cheaper to purchase than a smaller gas one, as are electric machines on the much larger end of the scale, but the middle ground occupied by most users favors gas. The direct firing process used by the gas ovens makes the process more efficient, thus cheaper overall. This is even true when a manufacturer has to install a gas service from scratch, with that one-time installation fee being less than the long-term cost of running an electric oven. Factor #2: Electric ovens, however, are more efficient at lower temperatures When you know you need to limit the temperature inside the burner to a lower level, then electric ovens have a major advantage. A gas oven is much less efficient in this regard, as you have to keep the temperature at a minimum level for it to stay working. The result is the need for the burner to cycle on and off while you keep relighting. The entire process is rather tiresome. An electric oven does not have this problem, since you can adjust the temperature to whatever you need without halting the movement of air. When temperature needs to be both precise and adjustable, electric is a good way to go. Factor #3: Gas ovens come with additional safety concerns One more advantage of electric ovens is safety. Gas ovens, regardless of their size, require explosion relief. Their direct-fired operation style means that the risk of explosion, no matter how small when running properly, is always present. That means mitigation by the proper incorporation of explosion relief, which adds to the initial costs. Factor #4: Different locations have different safety requirements If your operations are in a single location, then you only have to worry about local laws and regulations, but if you are purchasing equipment for other sites, especially international sites, then there are further rules to consider. Take Canada, for instance. In the Great White North, they have far stricter codes for gas ovens, which often will require third-party compliance inspections, and the machines will need ETL-C listings. That adds to the cost of doing business if you want gas ovens. In Summary In the end, you have to consider your own operational needs. The mid-size ovens that most industries need are most efficient in the gas form and if that’s the bottom line for you, then gas is best. Don’t forget the safety considerations, though. If, however, you need a small or very large unit, or operate at lower temperatures frequently, then electric suits you best. Connect with us today to learn more about our industrial finishing systems.
During these extremely trying and challenging times of lockdown and social distancing, a number of businesses and enterprises are being dubbed “essential services” and allowed to remain open. Auto body shops and their suppliers are such businesses. This means that if you want to operate safely, you’ll need to learn how to properly clean and sanitize your Accudraft paint booths. Not doing so can make your workplace hazardous for employees, and risk the spread of this deadly virus and disease. Using guidelines published by the Center for Disease Control and Prevention (CDC), we will share with you the best practices to adopt in cleaning your paint booth and keeping your work environment sanitary and safe. Stage 1 of Sanitization – Cleaning your facility Here are the important facts to remember about the stage 1 cleaning process: Conduct all your cleaning while wearing disposable gloves to ensure you don’t contaminate your hands. Start by setting up and executing a regular cleaning rota for all surfaces using soap and water (for sensitive parts like screens/keyboards etc., see “Considerations”). Focus your regular cleaning efforts on frequently touched surfaces, such as counter tops, door knobs, bathroom doors etc. Anything that’s safe to be cleaned with soap and water should be, especially any zone that is frequently touched. Stage 2 of Sanitization – Disinfecting your facility Once your work areas are clean, it’s time to start the crucial disinfecting process. Whatever tools you are using (see below), ensure that they are not expired, and safe to use indoors. As with the cleaning process, it’s important to prioritize those areas that are frequently touched: Best product to use is an EPA-registered disinfectant that’s certain to be effective against the virus SARS-CoV-2. In the absence of these, a typical diluted household bleach will also do the trick, but ensure you follow dilution instructions properly to gain the optimal effect. Leave disinfectant on the surface for at least a minute to work (or for whatever time instructed on the packaging). Considerations Readiness for the first two stages is the bulk of your work in cleaning your workspace, but there are some special considerations, especially for operators of paint booths. 1. Electronics --- things like touchscreens, keyboards, key controls and switches that can’t be washed in soapy water can be cleaned with disinfecting wipes. We advise that you use some kind of wipeable cover or case over these sensitive parts so you can quickly and effectively wipe them down with some alcohol-based wipe or other product. 2. Laundry --- keep any rags, cloths or towels you have in your shop in separate clean, wipeable containers or hampers for dirty/clean items. Wear gloves when putting dirty items in the laundry, and don’t shake them out in the open workspace. Remember to disinfect all containers regularly. 3. Staff Training --- the final key to making it all work is to establish procedures and then train your staff rigorously. For example, make sure every team member knows what to do in the event that another team member becomes sick --- open up exterior windows and then close off the interior doors to let air circulate; after 24 hours, go in to clean and disinfect all surfaces before closing off again. As we face a previously unknown disease, the scariest thing is not knowing what to do when things go wrong. Follow our guidelines and you’ll keep your essential workspace safe for yourself and your staff. Stay safe! Contact us to learn more.
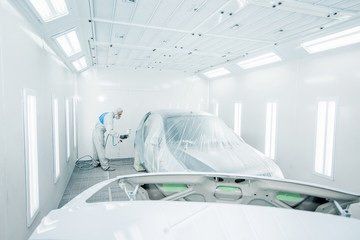
If you’re starting up a new auto shop and you’ve never bought a paint booth before, then choosing the right one to suit your needs can be tricky. You might not even be a start-up, but an established business in which you now face a choice in purchasing new equipment. Whatever your circumstances, choosing a new paint booth should never be done lightly. What you need most is good information, especially on the different airflow models that exist, and their advantages and disadvantages. See our guide below and you should be able to pinpoint which type of paint booth will work best for you: Crossdraft Booths This booth pushes air directly across the vehicle being painted. They are certainly the most popular, and arguably economical, paint booth type you’ll find on the market today. Air us drawn directly through its main doors or filtered columns in the front corners, and exhaust is sent through the back wall. Pros : Greater economy because its construction and installation require the least amount of material. No need for upper plenum construction needed in other booth types. Does not require downdraft pits or other concrete-built additions. You can lay a crossdraft booth right on your shop floor and it’ll work normally. Cons: Contaminants are more likely to land somewhere on the paint finish because it has to traverse the distance of the entire vehicle before it can exit. Painter can be exposed to substances unless they stand only at the front entry doors as paint overspray is forced to the rear. Semi Downdraft Booths These operate in a similar fashion to crossdraft booths, with exhaust and overspray exiting through the rear. Incoming air, however, it brought in via a small ceiling section at the front of the booth, which creates a diagonal draft pattern. Pros: Downward diagonal airflow is somewhat more effective than the crossdraft model, drawing contaminants away. Equally economical as the crossdraft due to no additional concrete building additions being required. Cons: The downward diagonal air flow can create a “dead zone” at the front end where little or no airflow can reach. Painter still at risk of exposure, and if overspray starts to swirl up in the dead zone, it can pick up additional contaminants and lay them on the paint finish. Side Draft Booths In this booth type, air is introduced through the ceiling and expelled through the side walls. The entire ceiling and all side walls are, therefore, filtered for exhaust purposes. Pros: The side draft creates a pleasing and even airflow pattern, which works to draw contaminants away from the paint finish --- this delivers better results. Once again, the side draft booths do not require additional concrete pits, making them suitable for shops needing faster and convenient installation. Cons: They are initially far more expensive than their counterparts because they need upper plenum construction above the workspace. Additional work includes side-wall duct work, and exhaust fans. In all, more material needed adds to the costs. Downdraft Booths In the downdraft booth, the draft pattern moves straight down from ceiling to floor. This type of booth may require raising up with drive-up ramps, or the installation of concrete pits, but there are numerous advantages that offset this initial inconvenience: Pros: With air drawn from the ceiling straight down over the ceiling and exhausted through the floor, the biggest pro is how clean you can keep each job. Overspray and contaminants are always pulled down, no matter what angle they are first sprayed on by the painter. The result is cleaner finishes, with much less need for buffing, polishing and any other correcting of imperfections after the job is done. Cons: The main drawback with downdraft booths is always the cost. Because it needs either concrete pits or raising on a steel basement, the initial cost will be greater. These costs can be offset by the quality of outcome, though. You Get What You Pay For In the end, you must ask yourself how much you are willing to initially invest in your paint booth to ensure the best results. That’s why we at Ecotech Systems like to recommend the Accudraft booths, which maximize the pros and minimize the cons mentioned above. Talk to us today about your paint booth needs and we’ll help steer you in the right direction.