5 Tips to Reduce Powder Coating Waste
5 Tips for Reducing Waste when Powder Coating
For any functioning business, the only line that matters is the bottom line. One of the things that greatly impacts your bottom line is waste, and this is something understood very well by those in the world of powder coating.
It seems that no matter how you work, things tend to get a bit messy when you’re powder coating something. Even though the amount of waste per item coated may seem infinitesimal, but the issue is when you multiply that waste by the high volume of items that you are coating.
Fortunately, there are five things you can do to reduce this waste, thus streamlining your entire operation and boosting your bottom line:
1. Install powder drawers
A simple yet novel solution to the issue of waste, removable powder drawers sit under the filters, catching powder after each pulse. Once the job is done, you can just tip the drawers into a storage drum or other unit and then transported. You may not be able to reclaim a great deal of the powder, but the time savings on cleanup are very significant.
2. Use pulse control
This technology is an optional addition to the powder collection modules. It’s simple yet impacting, giving much better and more consistent airflow and visibility within the paint booth. It works in tandem with either the drawers mentioned above, or the fluidized powder beds mentioned below.
How does it work? The effect stems from a magnehelic gauge located on the side of the booth, which monitors drops in pressure within the booth. Once it reaches the preset level, the filters “pulse” --- shake, vibrate for a very short period --- which causes the powder to fall from the filter and down to either the fluidized bed or the drawer. A neat, high-tech solution.
3. Utilize fluidized powder beds
Given that the sheer variety and complexity of shapes make coating perfection impossible, you may find it hard to beat the industry average of 70 percent transfer efficiency. The more complex your part, the harder to avoid waste. One option to mitigate this, however, is fluidized beds, which filters out other parts leaving just powder on the surface, which you can reclaim.
4. Add transfer pumps
When you’re wanting to cut down on time wasted shoveling out waste powder from the floor, a simple solution is the installation of a transfer pump. The pump moves powder from the fluidized bed and dumps it into whatever storage container you’re using to catch and process waste powder.
If powder reclaim is your goal, then the pump can also be fitted with a filter that catches debris and any heavy sedimentary material that would otherwise leave you with impure and useless powder.
5. Control airflow with manual VFDs
A business dilemma exists in powder coating. When you increase airflow, you make the environment safer for the painter, but increase the chance of waste since the airflow pushes more powder away from the object. Conversely, reducing the airflow stops the waste, but creates an unacceptably hazardous environment for the painter.
The solution is using manual VFDs. These will allow you to adjust airflow to match the situation. Turn it up when the work is done to remove the cloud of particles that remain behind, but turn it down while the all-important paint work is happening.
Follow our tips for an efficient, profitable and better-functioning powder coating operation. When you need help with your paint booths and related systems, you should look no further than Ecotech. We’re on hand to make your operation better and better. Connect with us to learn more.
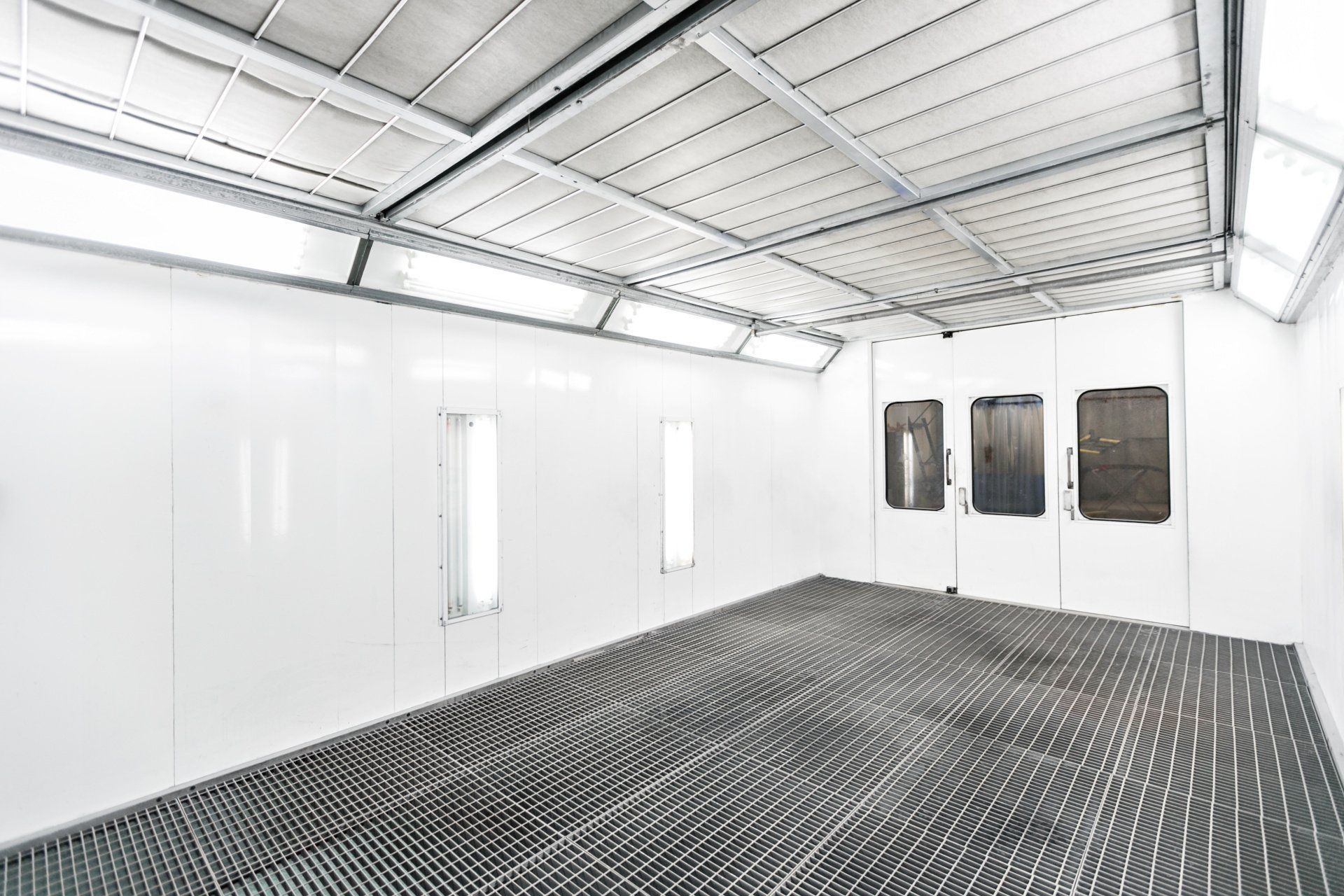
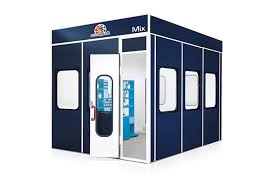
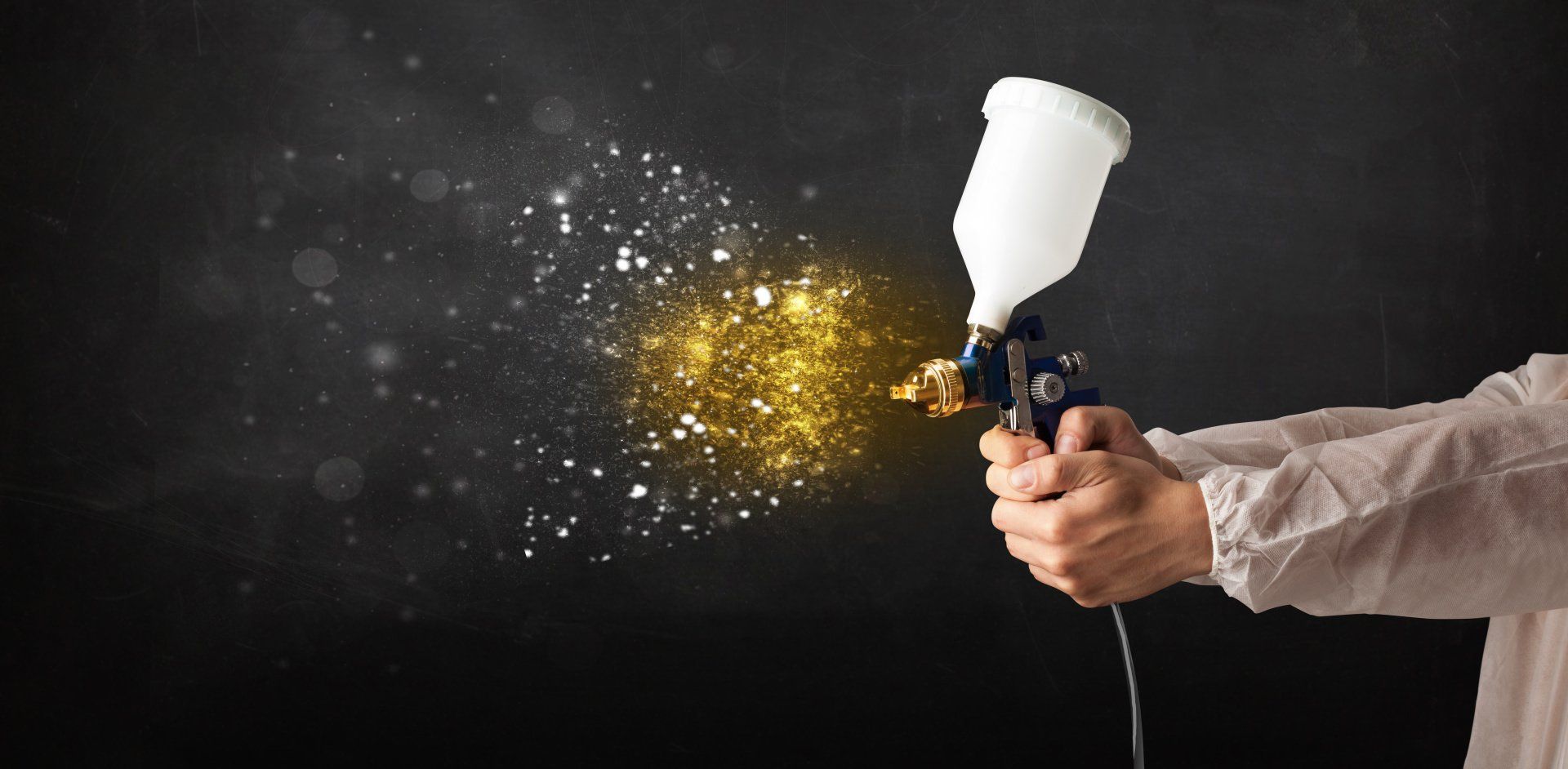
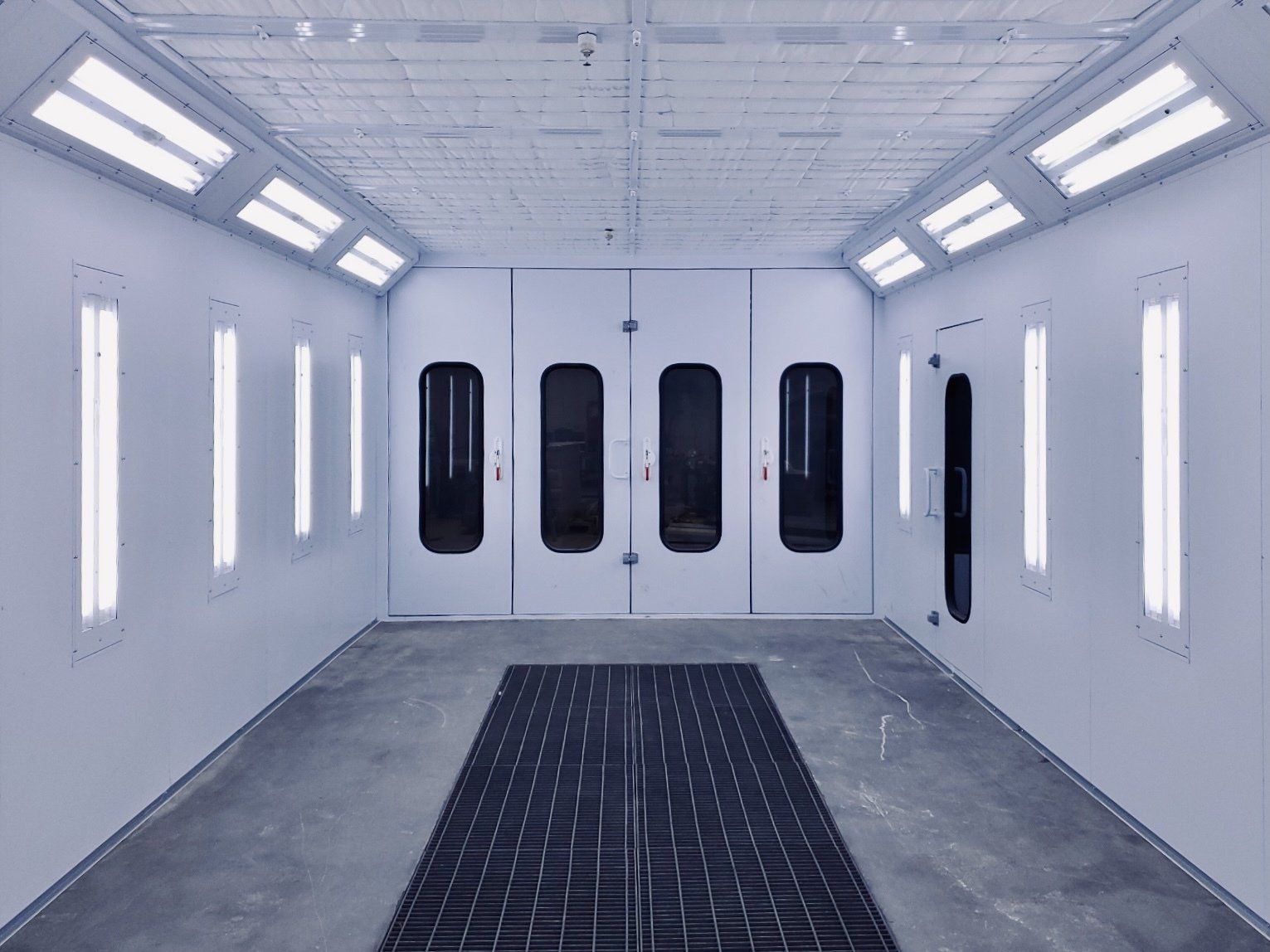
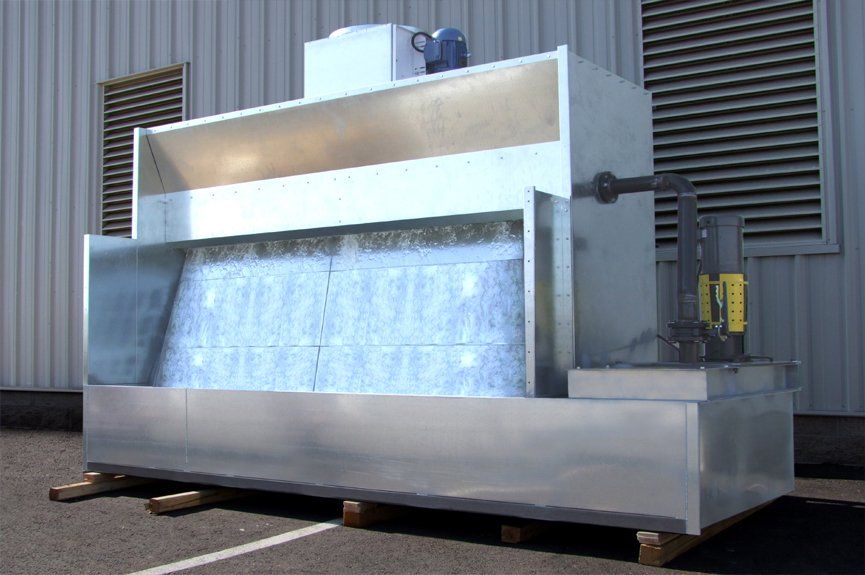

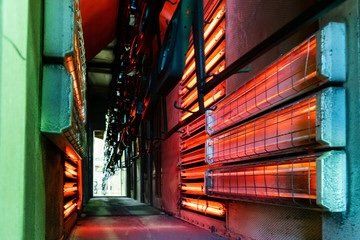
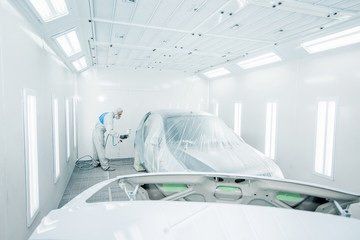